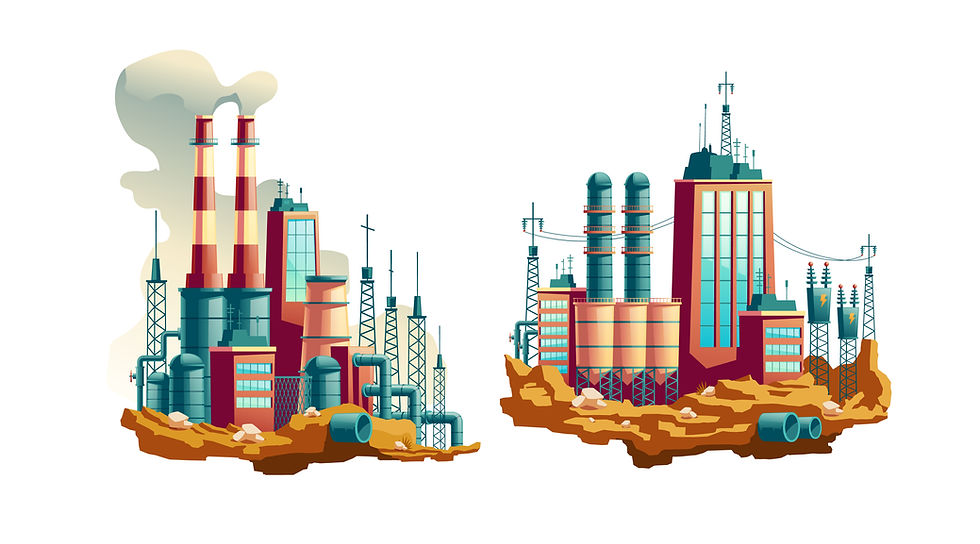
Classification of refractory materials Refractory materials are classified in various ways according to (i) chemical composition, (ii) chemical properties of their constituent substances, (iii) according to the place of use, (iv) refractory material, (v) manufacturing method, and (vi) The physical form, (vii) according to the application, (viii) according to the thermal conductivity, (ix) according to the main characteristics of the matrix, or (x) according to the compactness.
Classification according to the chemical properties of their constituent substances Refractories are usually classified according to the chemical behavior of their constituent substances, that is, their reaction to the type of slag . According to this classification, refractories are divided into three types, namely (i) acidic refractories, (ii) alkaline refractories and (iii) neutral refractories. There are also some special types of refractory materials.
Acidic refractories: These refractories will be corroded by alkali (alkali slag). They are used in areas where the slag and the atmosphere are acidic. Examples of acid refractories are silica refractories, zirconia refractories, and aluminosilicate refractories.
Alkaline refractories: Alkaline refractories are those that are corroded by acid slag at high temperatures but are stable to alkaline slag, powder and smoke. Since they do not react with alkaline slag, these refractories are very important for furnace linings in alkaline environments (such as steelmaking operations). The most important basic refractories are magnesite refractories, dolomite refractories and magnesia chromium refractories.
Nuetral refractory: It is a refractory material that is not affected by acidic or alkaline slags. Here are some examples: 1. Graphite (inert) 2. Chromite 3. Artificial refractory materials such as zirconium carbide and silicon carbide (which react with the main screw depending on the oxidation state and the type of material joining). Of these, graphite is the least reactive and is widely used in metallurgical furnaces, where the oxidation process can be controlled.
Classified by place of use: The iron and steel industry is the main consumer of refractory materials, and the industry consumes about 70% of refractory materials. Different areas of the manufacturing process in the steel industry are exposed to different temperatures, slag, and sulfur-containing gases. The diversity of operating conditions of different equipment puts forward different levels of requirements for different application fields. In addition, each production workshop has refractory materials that require special shapes and technical specifications required to meet the workshop process requirements. Therefore, refractory materials are often named after shops. Under this classification, refractories are divided into (i) refractories for coke ovens, (ii) refractories for blast furnaces, (iii) refractories for steelmaking, (iv) refractories for ladle, (v) refractories for tundish Materials, (vi) refractory materials from calcining plants, and (vii) refractory materials from heating furnaces, etc.
Classification by refractoriness According to the nature of refractoriness, refractory materials are generally divided into four categories. They are (i) super tariffs, (ii) high tariffs, (iii) medium tariffs and (v) low tariffs. The PCE (High-Temperature Cone Equivalent) value of high-strength refractories varies from 33 to 38. The PCE (High-Temperature Cone Equivalent) value of high-strength refractories varies between 30 and 33. Intermediate service refractories have a PCE (high-temperature cone equivalent)) value ranging from 28 to 30, while inefficient refractories have a PCE (high-temperature cone equivalent) value ranging from 19 to 28.
Refractory materials classified according to the manufacturing method can be manufactured by a variety of methods, including (i) dry pressing process, (ii) casting process, (iii) manual casting process, (iv) uniform molding in normal, mature or chemical agglomerates Craft. (v) Unshaped refractory materials, such as monoliths, plastics, tamping materials, guns and castables, etc. And classify accordingly.
Classified by physical form Refractories are classified according to their physical form. These are shaped and amorphous refractories. The shape is usually called refractory brick, and the unshaped one is called an integral refractory brick. Shaped refractories are those refractories that have a fixed shape when delivered to the user. Special-shaped refractories are commonly called refractory bricks. Brick shapes are generally divided into two types (i) standard shapes and (ii) special shapes. The size of the standard shape is suitable for most refractory manufacturers and is usually suitable for the same type of furnace and furnace.
The special shape is specially made for specific kilns and ovens. This may not apply to other ovens or the same type of oven. Molded refractories are almost always machine pressed, so a high degree of uniformity in performance is expected. Special shapes are usually formed by hand, and it is expected that their properties will be slightly different.
Unshaped refractories do not have a definite shape, but are formed during application. They form a seamless lining, better known as monolithic refractories. These are divided into plastic refractories, tamping mixtures, castables, gun mixtures, deburring mixtures and mortars.
According to the application classification, The chemical characteristics of the kiln process usually determine the type of refractory required. In theory, acidic refractories should not be used in contact with slag, gas, and alkaline fumes, while alkaline refractories are best used in alkaline environments. In reality, these rules are often violated for various reasons.
Classification according to the characteristics of the main base According to the characteristics of the main base, there are two types of refractory materials. The first is the refractory containing oxides. They are mainly oxides and their compounds. The most important oxides are Al2O3, CaO, MgO, SiO2, Cr2O3 and ZrO2. The second is a refractory that does not contain oxides. Examples of non-oxide refractories are refractories based on carbon and carbides, nitrides, borides and silicides. This group also includes silicones, which are sinterable derivatives of silicon nitride.
Classification based on compactness According to this classification, there are two types of refractories. The first type consists of dense refractory materials with an actual porosity of less than 45%. The second type consists of insulating refractory materials with an actual porosity greater than 45%.
Comments